ELECTRICAL
Maintenance and Servicing
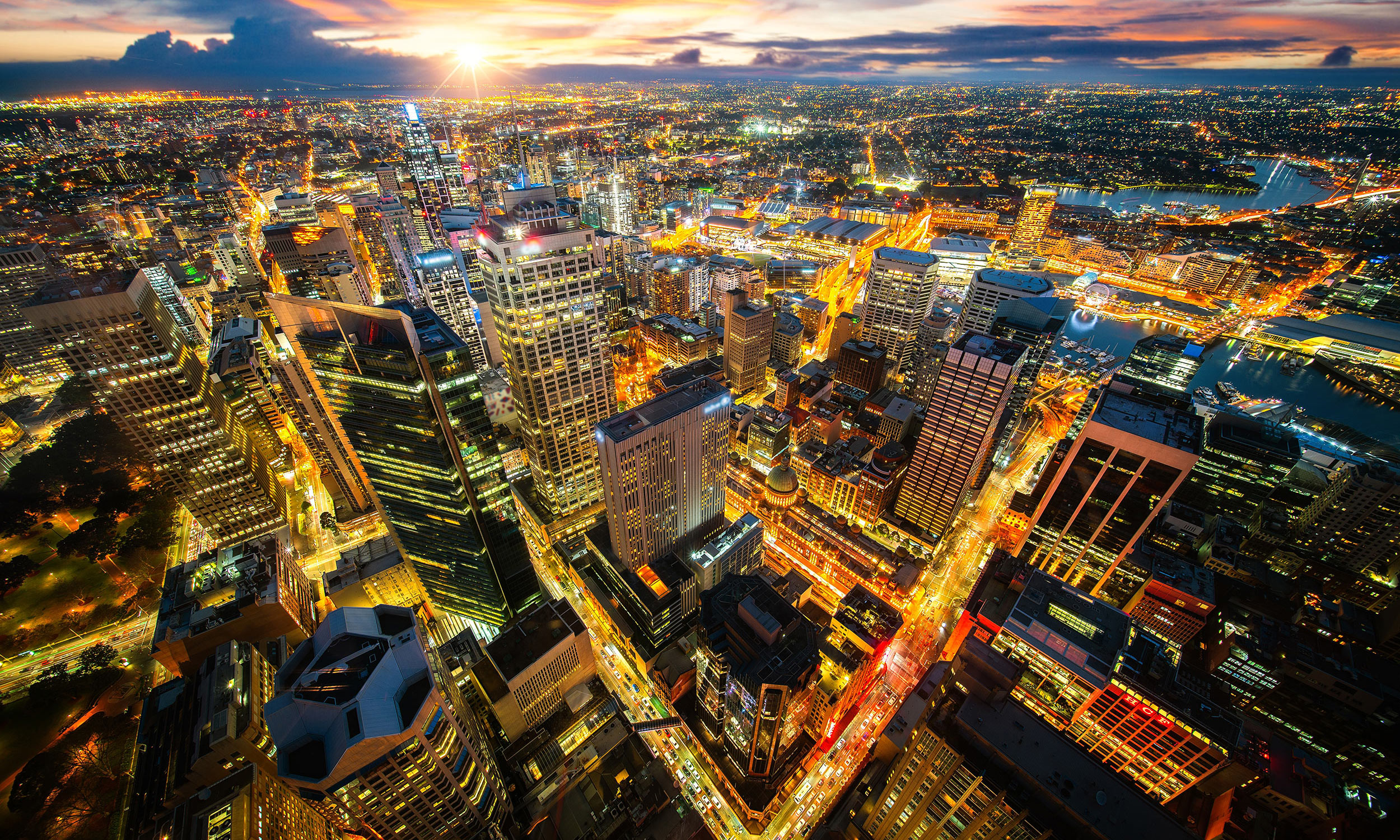
Powering Excellence, Delivering Reliability
Our team is made up of qualified and experienced licensed electricians and ACMA registered communications technicians, many of whom have been with us for more than 15 years. When you choose Rotric, you get a dedicated team member committed to excellence – we never subcontract our work.
We believe in transparency and trust. Whether you need a detailed, itemised quote or prefer working from an agreed schedule of rates, we ensure fair, competitive pricing so you can compare options with confidence.
Rotric maintenance services include:
- RCD Testing
- Electrical Test & Tag
- Exit & Emergency Testing
- Lighting Maintenance
- Switchboard Maintenance
- Thermographic Testing
- Power Factor Correction Testing
- Generator Maintenance
- Minor Works
- Service, Repairs & Maintenance
Who must manage electrical risks?
A person conducting a business or undertaking has the primary duty under the WHS Act to ensure, so far as is reasonably practicable, that workers and other persons at the workplace are not exposed to electrical risks arising from the business or undertaking. This duty requires eliminating electrical risks or, if that is not reasonably practicable, minimising the risks so far as is reasonably practicable.
A copy of the NSW Governments – WorkCover Code of Practice for Managing Electrical risks in the workplace is available @ http://www.workcover.nsw.gov.au/__data/assets/pdf_file/0019/15580/managing-electrical-risks-code-practice-3836.pdf
Inspecting and testing equipment
Regulation 150 (WHS Regulations)
A person conducting a business or undertaking with management or control of electrical equipment must ensure that the electrical equipment is regularly inspected and tested by a competent person if the electrical equipment is;
- Supplied with electricity through an electrical socket outlet (‘plug in’ equipment); and
Used in an environment in which its normal use exposes the equipment to operating conditions that are likely to result in damage to the equipment or a reduction in its expected life span
This includes conditions that involve exposing the electrical equipment to moisture, heat, vibration, mechanical damage, corrosive chemicals or dust.
Inspecting and testing RCDs
Regulation 165 (WHS Regulations)
A person with management or control of a workplace must take all reasonable steps to ensure that residual current devices use at the workplace are tested regularly by a competent person to ensure the devices are working effectively.
Residual Current Device (RCD) Testing
RCDs are tested in accordance with Appendix H of AS/NZS 3760:2022.
The operating time of RCDs is checked against acceptable maximum values to ensure they’re functioning correctly and providing the added safety measure.
Testing and inspection intervals are outlined in Table 4 of the Standard, with the length of time dependant on the type of environment and/or equipment, or as varied by a responsible person based on risk assessment.
For most commercial office spaces there will be a combination of environments deemed hostile (kitchen, workshop etc.) and not hostile (stationary/printing room, workstations etc.) the time frame for the former being a 12 month interval, the latter a 2 year interval, at Rotric we recommend a uniform testing interval of 12 months as the additional testing is usually immaterial and confirms safe operation of all RCDs in the workplace.
AS/NZS 3760:2022 In-service safety inspection and testing of electrical equipment and RCDs
Inspecting and testing electrical equipment
Regular testing can detect electrical faults and deterioration that cannot be detected by visual inspection.
The testing interval provided by this standard is dependent upon the workplace environment being either hostile or not hostile; however, the intervals are 12 months and 5 years. An amount of discretion for the interval is given and can be varied by a responsible person based on risk assessment.
AS/NZS 2293.2:2019 Emergency lighting and exit signs for buildings, Part 2: Routine service and maintenance
A requirement of this Standard to maintain compliance is a six-monthly battery backup test for exit and emergency light fittings in the workplace.
This is undertaken by operating the self-contained emergency luminaires and exit signs from their battery supply by simulating failure of the monitored supply. The luminaires and exit signs shall remain illuminated for not less than 90 mins or such longer period as may be required by the building regulations.